On July 10th, the NJDOT Bureau of Research hosted a Lunchtime Tech Talk! webinar, “Advanced Reinforced Concrete Materials for Transportation Infrastructure.” Welcoming remarks were given by Mansi Shah, Manager of the Bureau of Research, who turned over the session to its moderator, Omid Sarmad, a member of the NJDOT Technology Transfer Project Team. The presentation was conducted jointly by the Co-Directors of New Jersey Institute of Technology’s Materials and Structures Laboratory (MATSLAB), Dr. Matthew Bandelt, and Dr. Matthew Adams.
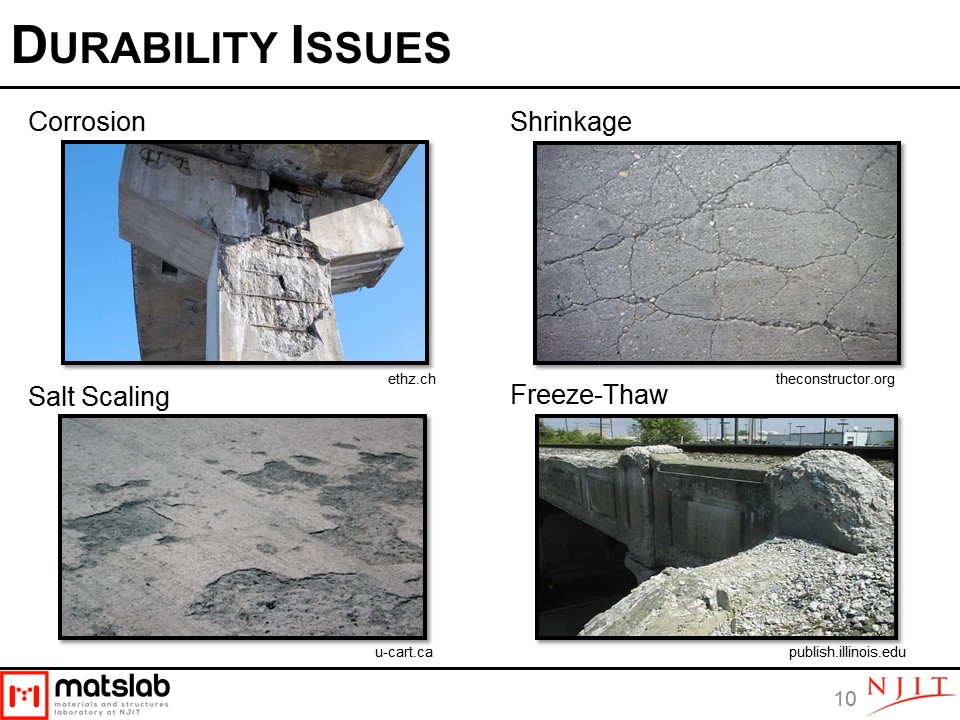
Transportation infrastructure systems must resist conditioning from the natural environment and physical demands from service loading to meet the needs of users across the state. Deterioration leads to costly and timely durability and maintenance challenges. This presentation provided a background on the state-of-the-art of advanced reinforced concrete materials that are being investigated to improve reinforced concrete transportation infrastructure. The duo, both Associate Professors at the New Jersey Institute of Technology, spoke about the team’s research conducted to assess the mechanical properties and long-term durability of these systems.
Dr. Bandelt opened the presentation with an overview of the MATSLAB where the work was conducted, and the motivation which led to the project. The demand for the research was initiated by the various durability issues that exist in concrete, in particular corrosion, shrinkage, salt scaling, and freeze-thaw cycles. These issues are exacerbated in New Jersey due to the climate and the large-scale adoption of concrete throughout the state. A variety of different concretes were evaluated in the project, such as Ultra-High Performance Concrete (UHPC), Engineered Cementitious Composite (ECC) and a Hybrid Fiber Reinforced Concrete (HyFRC), each having its own unique mechanical properties.
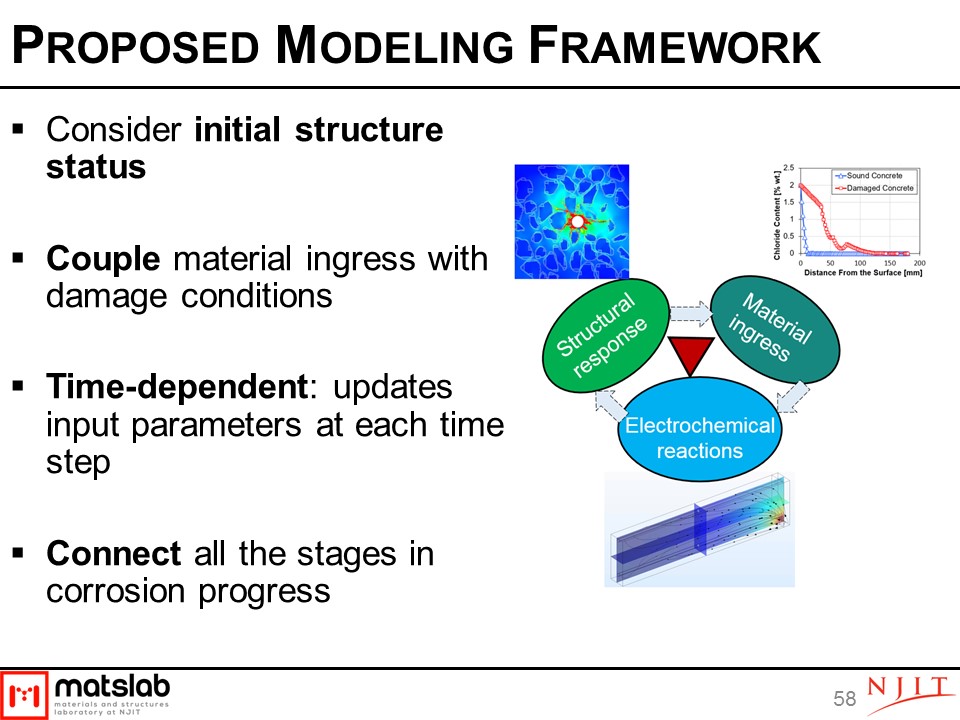
The experimental testing program involved mechanical testing, corrosion testing, testing in freezing environments, and shrinkage testing. Corrosion testing of ductile and normal concrete systems used a chloride ponding test method with exposure to an aggressive environment for over one year. Various steel reinforcing bars were studied, and systems were tested in uncracked and pre-cracked conditions. Freeze-thaw and salt-scaling experimental activities were conducted, using mixes that were commonly used by NJDOT. Drying shrinkage behavior of the ductile and normal concrete systems was also investigated. Dr. Bandelt and Adams developed a numerical modeling approach to simulate the corrosion behavior of ductile concrete systems to understand the long-term performance. The results of the durability testing showed that UHPC had the best performance across the board, and that ductile concrete systems had improved durability.
The professors then described their life-cycle cost modeling methodology, which was completed to assess the costs of a representative bridge-deck made with normal reinforced concrete. There are primarily two ways to evaluate service life; experimental evaluation which describes the physical testing of materials is accurate and intuitive, while numerical evaluation is more cost efficient, time efficient, and more easily extrapolated to various scenarios. There are gaps however in numerical modeling, mainly the lack of inclusion of cracks, corrosion behavior, and boundary conditions. The team sought to develop a framework to simulate the long-term durability of a select group of materials under the combined effects of mechanical loading and environmental conditioning.
The research showed that their framework was effective in service life evaluation, and that most importantly, UHPC bridge deck experienced slower deterioration under the same traffic load and environmental conditions. The reinforced UHPC beams and reinforced UHPC bridge decks exhibited excellent resistance to chloride penetration and corrosion propagation according to the modeling results. The structural deteriorations of the reinforced UHPC systems were also significantly slower compared to that of reinforced normal strength concrete systems. The study also showed that chloride induced corrosion performance is affected by the initial damage pattern, which depends on the structure and loading conditions. This means that it becomes important to consider the structural configuration, traffic loading conditions, and climate characteristics to assess the long-term durability of an advanced reinforced concrete system.
Afterwards, Dr. Bandelt and Adams both participated in a Q&A with the audience.
Q. UHPC seems to be advancing in the bridge industry. What are the biggest challenges looking forward on the rehabilitation of bridge decks?
A. Yes, it’s advancing quite rapidly. The FHWA has a website where you can see all the projects where UHPC was deployed, and if you plot the number of projects over time, you’ll see nearly an exponential growth. Part of that is due to the fact that there is a lot of research going on, and a lot new standards coming out. Organizations like AASHTO and ACI have released a lot of design guidance that has helped spur adaptation.
Still, the biggest challenge is getting new people used to using these design methods. As we move past some of that, I think we’ll see adoption continue to increase. UHPC may not be the right solution for every project, but there are many beneficial uses for which it will be the most appropriate tool to achieve long lasting sustainability.
Q. Regarding the resilience of concrete: Are advanced reinforced concretes better able to handle the freeze/thaw cycles that could be outcomes of climate change? If so, do you have any modeling projection to show how it fairs in comparison to regular concrete?
A. We haven’t done any specific modeling in comparison to traditional concrete in relation to climate change, but in general these systems are more resilient. They simply perform better; as you saw in our research, after 300 cycles we saw virtually no damage from freeze/thaw cycles in the system. When you see that level of performance in these accelerated tests which are quite aggressive, you can extrapolate that these advanced reinforced concretes will simply perform better.
Q. Why did the HyFRC showed much higher free shrinkage than HPC? Is the HyFRC mix design different from HPC other than fibers?
A. The mix design of the HyFRC is a bit different. One thing in particular is that even though it has those blended fibers, it has a significantly higher water to cement ratio. So because it has more water, it is a bit more prone to drying shrinkage. With UHPC that turns out to be less of a concern because it’s much stronger and is not as susceptible.
Q. Could your modeling adjust relative humidity to a more wet and hot climate in the future?
A. Yes, absolutely. The case study we looked up was in New Jersey, but we can modify that to be in any setting so you can see where it would be geographically advantageous to use certain systems.
Q. Can you explain more about the deterioration we saw in slide 66?
Advanced Reinforced Concrete Materials for Transportation.
A. Basically what we did was look at tensile strains throughout a bridge area. The colors coincide with different levels of tensile strain. We counted up areas that were in different sections, and based on the percent area that we saw that was damaged, and we would use a multiplier to create a rating system.
To view a copy of the presentation, please click here.
Resources
Bandelt, M., Adams, M., Wang, H., Najm, H., and Bechtel A., Shirkorshidi, S., Jin, F. (2023). Advanced Reinforced Concrete Materials for Transportation Infrastructure [Final Report]. Retrieved from: https://www.njdottechtransfer.net/wp-content/uploads/2023/05/FHWA-NJ-2023-003.pdf
Bandelt, M., Adams, M., Wang, H., Najm, H., and Bechtel A., Shirkorshidi, S., Jin, F. (2023). Advanced Reinforced Concrete Materials for Transportation Infrastructure [Technical Brief]. Retrieved from: https://www.njdottechtransfer.net/wp-content/uploads/2023/05/FHWA-NJ-2023-003-TBFINAL.pdf