On November 14, 2019, FHWA sponsored an innovation exchange webinar, "The Connected Job Site," that was live broadcast by the NJDOT Bureau of Research as part of its Tech Talk! series, for NJDOT staff at NJDOT Headquarters in the Foran Building Training Room.
With the recent influx of new technologies such as smartphones, tablets, and drones, and their growing and widespread availability, many ingenious applications have been developed for their effective deployment in construction and operations and maintenance activities in transportation. These technologies have allowed for real-time project monitoring, improved communication among team members, documentation stored on the cloud, and more efficient online scheduling. During this webinar, attendees learned about what exactly connected job sites are, and how various local agencies from around the country have started to utilize these technologies in innovative ways.
FHWA launched the webinar with a short presentation, Ten Examples of Connected Technologies, that highlighted examples of tools and technologies found on the connected job site. The primary objective behind the adoption of these connected technologies is to save time and money and improve safety in operations. Hardware like smartphones, tablets, laptops, wearable technology and various vehicles and equipment have streamlined communications and planning in performing field work, while software solutions like 3D Modeling and Building Information Modeling (BIM) have improved the accuracy and efficiency of digital representation for physical facilities and infrastructure design. Virtual reality (VR) technologies have also started to find applications in the field, allowing professionals to safely experiment and test ideas in an artificial environment and bring products and concepts to life through visualizations. Using VR in conjunction with drone technology, for example, has allowed maintenance crews to safely examine parts of bridges that were previously hazardous to inspect. The advent of unmanned aerial vehicle systems, in general, has provided the ability to garner visual information at a lower cost than traditional methods, while keeping workers out of harm’s way.
Connected job sites do not always have to deploy new technologies; sometimes they just re-purpose applications of older technologies in conjunction with new ideas. GPS systems have been around for decades, but when used with new software they are immensely effective in improving efficiency. Two case examples of this were provided by the local public agencies who participated in the webinar.
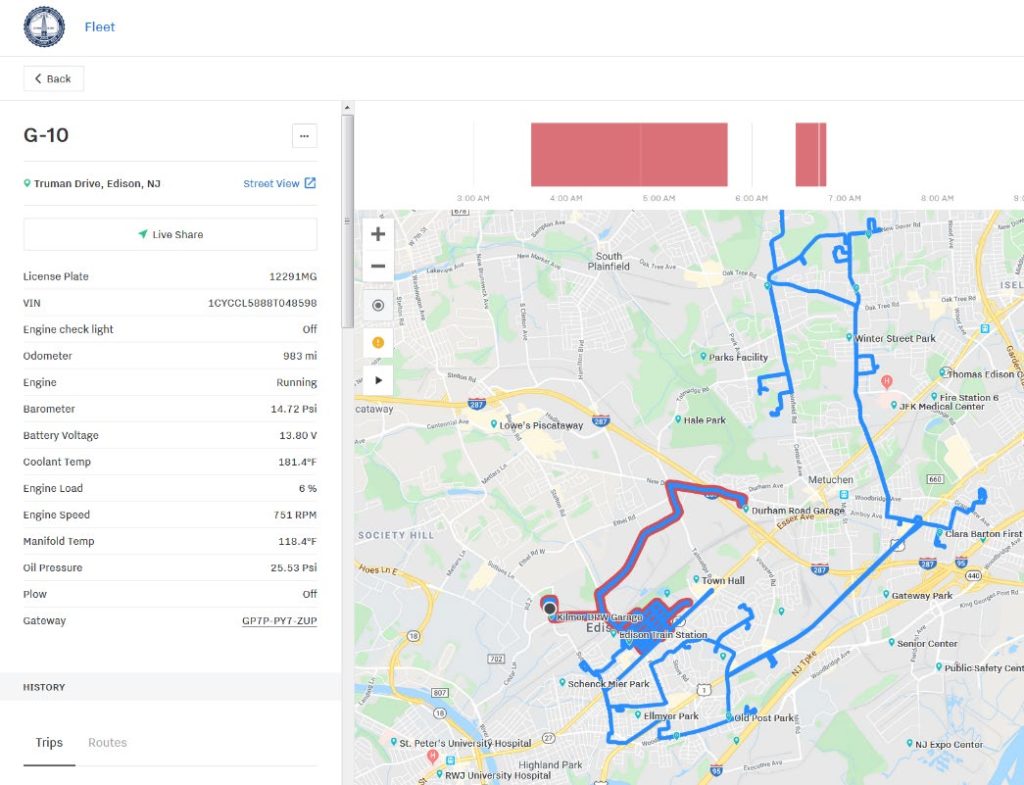
Township staff can review actual snow plow routes to improve cost-effective coverage and verify citizen complaints
The Township of Edison’s presentation, Improve Fleet Operations Through the Use of GPS and Telematics, provided by the New Jersey municipality’s Information Technology Manager, described some benefits and challenges of the installation of GPS tracking devices on its vehicle maintenance fleet. During snow events, the Township was able to monitor the entire routes taken by its snow plow trucks and the specific segments where the plows were used. Once the monitoring systems were in place, the Township found that it had the capability to more effectively evaluate individual citizen complaints of streets not being plowed adequately. For example, the Township could check its mapped records of fleet route deployment during storm events, and see if the complaints were "true" and then determine whether a specific snow removal job needed to be repeated. More broadly, the tool allowed the agency to ascertain whether designated routes were being followed by operators and whether the priority routes themselves were efficient and effective in both design and operation.
This capability had the added benefit of reducing the Township’s liability for alleged property damage. In fact, the Township found that some 50 percent of the claims that asserted that snow plows were hitting parked vehicles could not be substantiated after checking the GPS location of the snowplow trucks and their route history. Insurance claims and payouts were reduced by some 60 percent due to this capacity to technically validate the potential merits of a claim. The Township also found that it was able to improve efficiency in route designs, leading to less wear and tear on equipment, less use of salt and brine, and a reduction in person-hours and overtime costs.
The Township touched upon tool features that improved the monitoring of vehicles for preventative maintenance. As vehicles systems were now connected to a central hub, needed repairs were identified more quickly and systematically, and less dependent on individual driver reports of faults in a vehicle's operation. Eventually, low use and high maintenance cost vehicles were better identified and retired, allowing for an overall fleet reduction of 35 percent which, in turn, has reduced costs for fuel, insurance, parts and labor.
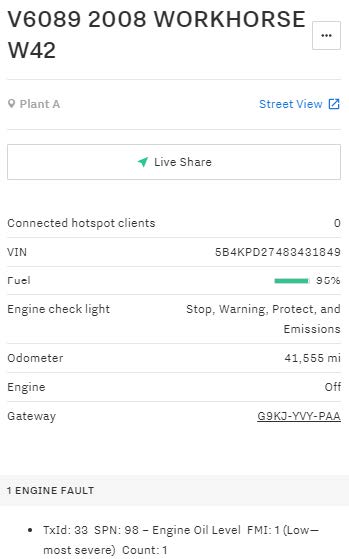
For Lauderdale uses available individual vehicle operations measures to improve safety and support preventative maintenance progam for its fleet.
The City of Fort Lauderdale’s presentation, How to Improve Fleet Sustainability, jointly given by the City’s Program Manager for Fleet Services and their Automotive and Equipment Specialist, described several features and benefits of their fleet management program, including the use of geofencing. A geofence is a virtual perimeter dynamically generated for a real-world geographic area around a point location, or a predefined set of boundaries. It is typically used for security purposes and to better track people and equipment. Fort Lauderdale used geofencing to help preserve its infrastructure, as it was able to monitor overweight trucks using historic bridges; with this real time technology, they were able to reduce over-weight vehicles crossing the bridge by nearly 90 percent.
Vehicle tracking had the side benefit of making their drivers operate more safely. The City found that its personnel were less likely to go over the speed limit if they were monitored, and “harsh events” such as braking and sharp turns were also reduced. Examples of some of the specific and aggregate dashboard performance measures that can be monitored for equipment usage were highlighted.
In the dialogue following both presentations, it was clear that the adoption of the connected technologies changed the way business is being performed. Notably, the tools and performance measures permit increased tracking of the workforce on-the-job. The presenters acknowledged that it can raise concerns about the level of monitoring available to the local public agency's management team. However, according to the presenters, the implementation of the systems has generally improved the safety and efficiency of daily operations and contributed to improved maintenance and longevity of their fleets.
While the webinar shared just a couple of case examples primarily focused on fleet management, the FHWA hosts stressed that the future of connected job sites will only grow as the “internet of things” becomes more complex. Everything from automated vehicles, intelligent compaction, drones, and RFID scanners will continue to find new applications, and new ways to save money and enhance safety.
The Connected Job Site webinar is one in a series of Innovation Exchange webinars sponsored by the Center for Local Aid Support (CLAS) in the Federal Highway Administration's Office of Innovative Program Delivery. Through Innovative Exchange webinars, CLAS seeks to bring cutting-edge transportation leaders to the table to share ideas and out of the box innovative practices that have proven results. More information about this webinar, upcoming webinars, and webinars available on demand can be found here.